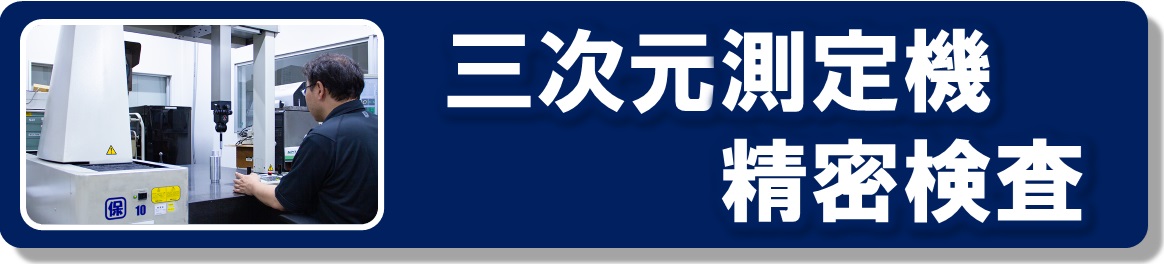
三次元測定機による精密検査の受託
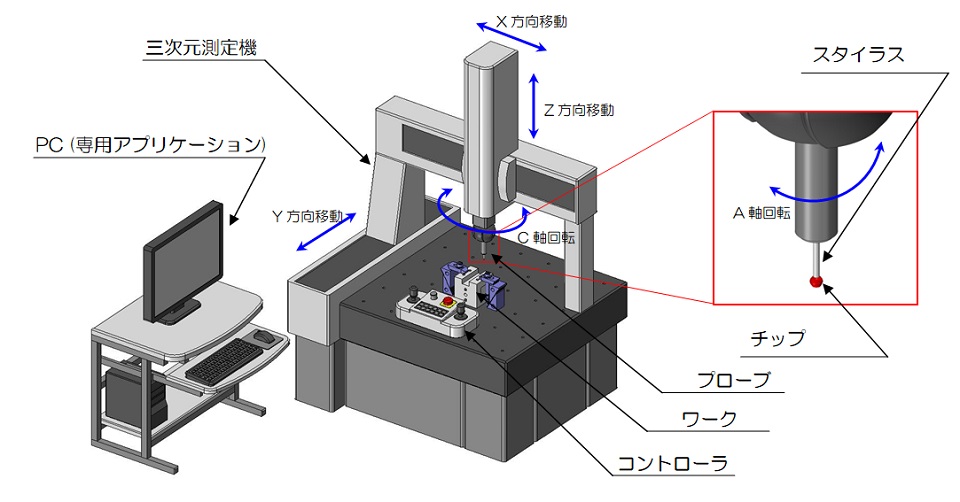
三次元測定機(CMM: Coordinate Measurement Machine)は、X軸、Y軸、Z軸に駆動する機構を備えた、精密測定用の機械です。
ヘッド先端には、測定するためのプローブを備えていて、プロープ先端(チップ)を製品に接触させることで、接触したポイントの三次元座標を認識し、記録します。
様々なポイントの座標情報を測定することで、平面や直径などを割り出し、さらには形状同士の位置関係などを算出することが可能となります。
このため、汎用の測定器具では測定できない幾何公差なども測定可能となります。
三次元測定機は非常に高価で、測定にも専門の技能が必要になります。
また、測定精度を保つために、一定の空調(おおむね20±1℃など)の効いた空間で使用することが必要で、振動が少なく剛性の高い地面に設置する必要があります。
三次元測定機で測れる要素
三次元測定機では、想定する要素を設定してから、その要素を確定するのに利用するポイントを測定していきます。
それぞれの要素と、その要素を確定するのに最低限必要なポイント数は下記のとおりです。
<要素> | <最小限必要なポイント数> | <算出される情報> |
点 | 1点 | 点データ (点のX,Y,Z座標値) |
線 | 2点 | 線データ (線のベクトル方向及び線上の任意の点) |
平面 | 3点 | 平面データ 法線データ |
円 | 3点 | 直径・半径 真円度 中心点位置 |
楕円 | 5点 | 楕円データ 長辺・短辺長さ 中心点位置 |
球 | 5点 | 直径・半径 中心点位置 |
円筒 | 6点 | 軸の線データ 直径・半径 円筒度 |
円錐 | 6点 | 軸の線データ 直径・半径 |
実際の測定では、これらの要素から算出される情報を組み合わせ、専用アプリケーション上で、検査に必要な項目の数値を取得していきます。
それぞれの要素の結果自体はもちろんですが、要素同士の三次元的な位置関係から、幾何公差を求める事が可能です。
例えば、「2つの円筒形状の測定結果から同軸度を取得する」、「2つの面の測定結果から垂直度を取得する」などという検査が可能となります。
また、それぞれの要素の確定に必要なポイント数は、上表の通りですが、ポイント数が多くなるほど測定精度が向上します。
通常、Φ50mmの円形状の測定には、8~20点程度のポイントを測定します。
ただし、必要以上に多くのポイントを取得しても測定精度が上がらないばかりか、工数ばかりが嵩みます。
形状に応じて、合理的なポイント数を検討するのが、ベテラン検査員の腕の見せ所と言えます。
三次元測定機による輪郭測定
三次元測定機は立体物の三次元空間における点位置を測定する事ができます。
測定した点の座標値を3次元CADデータと照合して、空間的な精度の確認を行う事が可能です。
このような3次元形状の輪郭測定は、ポイント照合などとも呼ばれ、自由曲面形状の多い航空機部品などで多く活用されます。
測定結果は、各ポイントの理論的な座標点と、実際に測定した測定値、理論点からの乖離具合を検査結果としてまとめて提出させていただきます。
三次元測定機の測定手順
STEP 1: 起動及びキャリブレーション
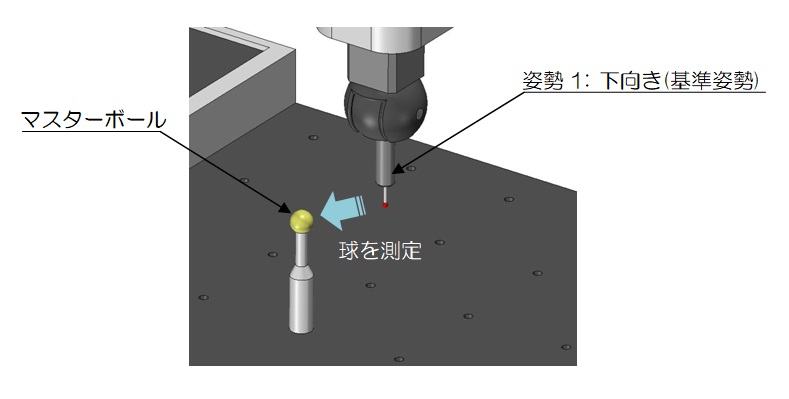
三次元測定機は、起動後に使用するスタイラスのキャリブレーションを行います。
チップの直径や、スタイラスの姿勢ごとの補正値を割り出す事になります。
具体的には左図のような、真球度の高い「マスターボール」を使用します。
マスターボールの球形状部分を「球」の要素として測定します。
これにより、チップの半径を割り出すことができ、測定の際にはこの半径分だけ補正してチップ中心位置の座標系を読み取ることができるようになります。
基本的にはこのスタイラスが真下を向いた姿勢が「基準姿勢」となります。
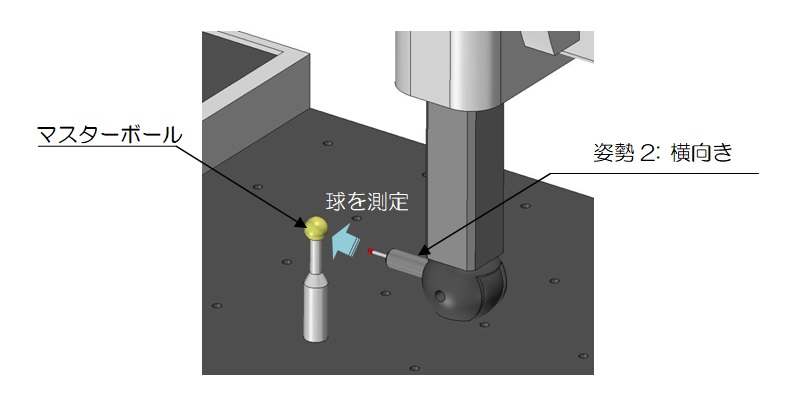
三次元測定機の多くの機種で、スタイラスの姿勢(A軸角度、B軸角度)を変更することができます。
スタイラスの姿勢を変える事で、基準姿勢では測定できない横穴などにもアクセスできるようになり、幾何公差の測定が可能となったり、段取り替えの手間が省けたりします。
姿勢を変えた状態で、再度キャリブレーションを行うことで、基準姿勢との相対的な位置関係を割り出すことができ、測定途中で姿勢を変えても基準を変えずに測定を続けることが可能となります。
STEP 2 : ワークの固定、座標系の定義
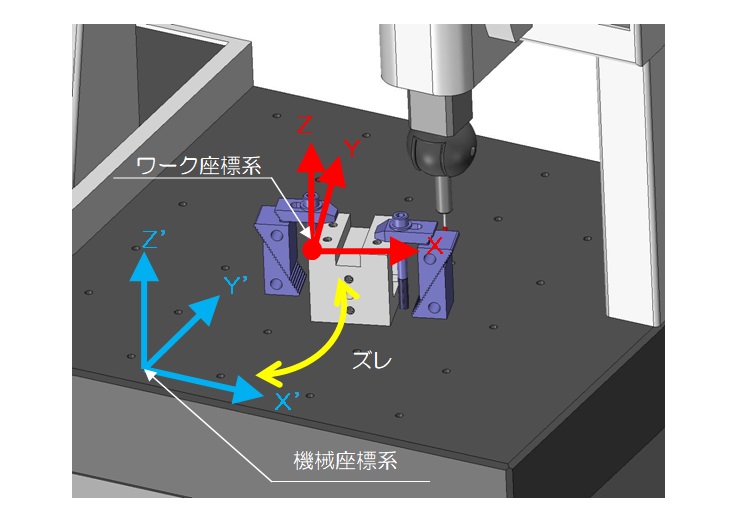
ワークを三次元測定機のテーブルに固定します。
通常の三次元測定では、切削加工のような強い力がかかりませんので、クランプ工具などで動かないように軽く固定する程度が一般的です。
次に、ワークの座標系を定義します。
三次元測定機自体の持っている機械座標系(X軸、Y軸、Z軸)と、ワークの座標系は異なりますので、ワークを基準とした座標系を改めて設定することが必要となります。
通常は図面に定義されているデータムを優先してワーク座標系を設定しますが、特に図面の指定がない場合は、オペレータの判断で任意に座標系を定義します。
通常の直交座標系では、座標系の定義として「原点」と「X軸、Y軸、Z軸のうち2軸」が必要となります。
「ワーク上面の画面から見て左下の角が原点」という設定で座標系の測定を進めていきましょう。
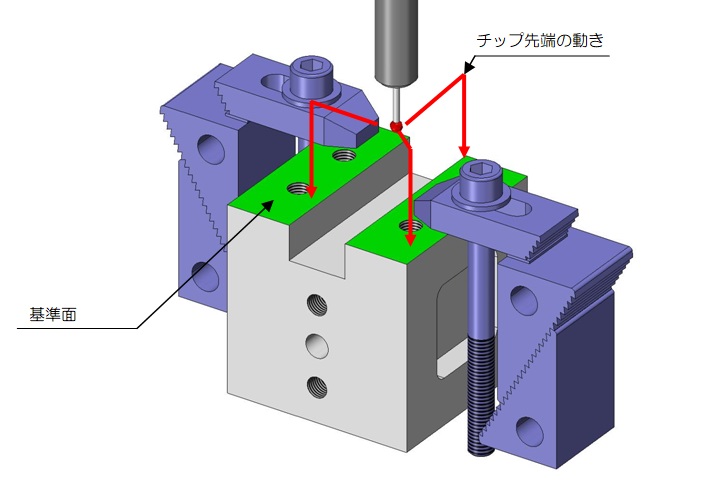
緑色の部分が基準面(Z基準)となりますので、この面にチップを触れさせ「平面」を測定します。
平面は3点以上触れる事で測定可能ですが、通常は10~20点程度のポイントを取得します。
取得した平面を、専用アプリケーション上で「基準面」として定義します。
これで、新しくワーク座標系の基準となる平面のデータを取得し定義することができました。
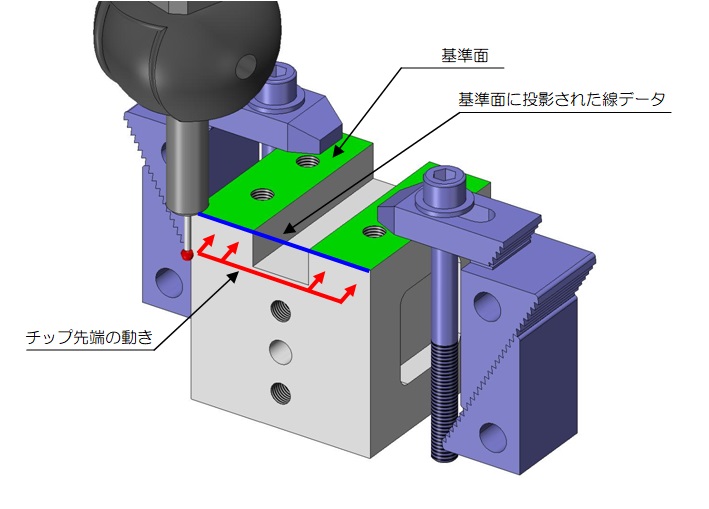
次に、ワーク座標系のX軸を定義していきます。
ワークの側面にチップ先端を当てていきます。
線を定義するためには2点以上のポイントが必要ですが、現実的には5~10点ほど取る事が多いと思います。
取得したポイントの座標系を専用アプリケーション中で先ほどの「基準面」に投影し、それを線データ(青)とします。
得られた線データを「X軸」に定義します。
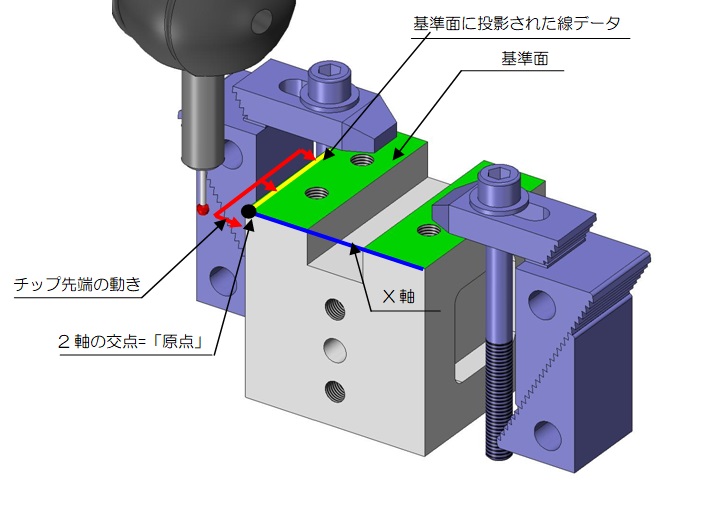
続いて、X軸と同様に画面から見て左奥側の側面にチップ先端を当てていきます。
取得したポイントの座標系を専用アプリケーション上の「基準面」に投影することで基準面上の線データ(黄色)を得ることができます。
そして先ほどのX軸(青)とこの線とが交差するポイントの座標値(黒点)を割り出します。
この黒い点がワーク座標系の原点となりますので、「原点」として設定し、座標系の構築が完了します。
以上のように、「基準面」、「基準軸」、「原点」を順に測定しながら設定していくことで、ワーク座標系を構築する事が「座標系の定義」となります。 ここまでで、測定前の準備が完了です。
STEP 3 : 測定
座標系の設定が完了したら、図面指示に基づいて各形状の測定を行います。
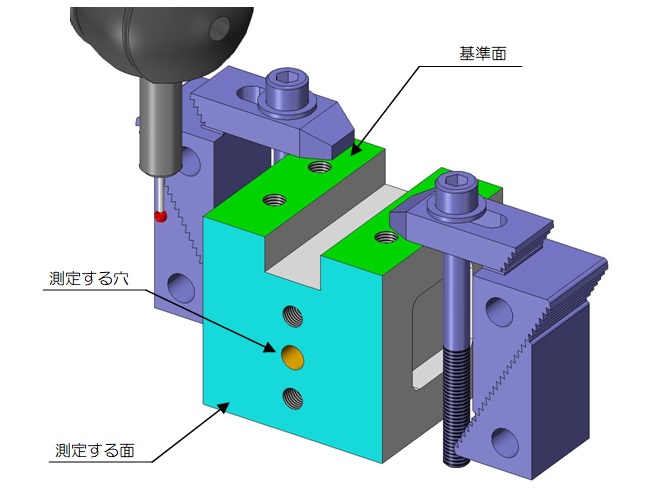
ここでは例として、「基準面」に対する水色の面の「直角度」と、水色の平面に対するオレンジ色の穴の「直角度」を測定する手順をご紹介します。
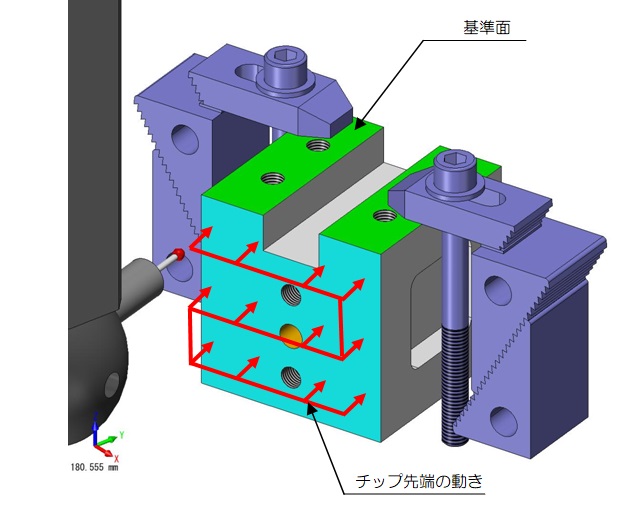
スタイラスを傾け(事前にキャリブレーションしておきます)、左図のようにチップ先端を側面に触れさせて「平面」を測定します。
これで専用アプリケーション上に記録されている「基準面」と今回取得した「平面」との直角度を算出することができます。
アプリケーション上でデータ同士を照合し、「直角度」を演算させます。
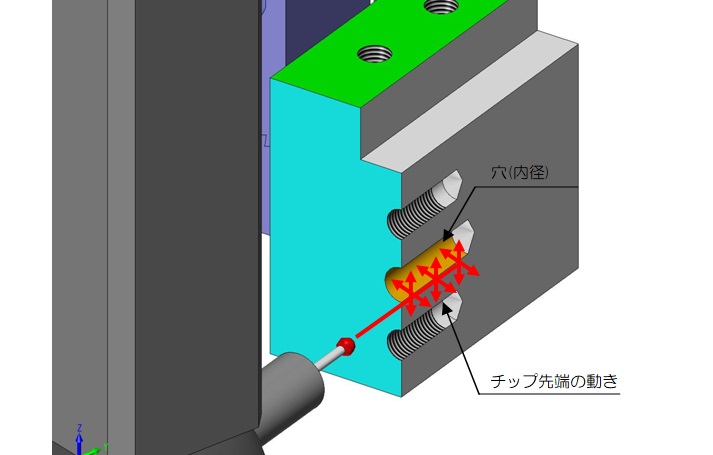
続いて穴の測定に移ります。
直角度を算出するためには、穴を「円筒」として測定し、中心軸の線データが必要となります。
スタイラスを穴に入れ、ある深さで穴の内径に数点触れて各ポイントの座標値を取得した後、さらに置く前入れて内径のポイントの座標系を取得します。
繊細な操作が必要な測定作業です。
円筒形状もできるだけ多くのポイントを取得することで、測定精度が向上します。
特に軸方向の情報が必要な場合は、奥行方向に3か所ほどは測定ポイントを設けます。
取得した「円筒」のデータに中心軸の線データが含まれますので、先ほどの「平面」と「円筒」との直角度を算出することが可能となります。
専用アプリケーション上で、直角度を演算させます。
また、円筒と平面の交線は、平面上の「円」となります。
この円を算出すると、円の中心点の情報も得ることができ、例えば基準点からの「位置度」の算出に利用することができるようになります。
このように、三次元測定機による測定では、測定データを蓄積しながら、要素ごとの三次元的な幾何公差や寸法値を割り出していくことが可能で、検査工程においては非常に強力なツールです。
このような幾何形状の測定の他にも、自由曲面上の点を測定し、その三次元座標を3Dモデルデータと照合する「ポイント照合」と呼ばれる測定も良く用いられます。
ポイント照合は、航空機部品の他、金型や成形品の検査などにも利用されます。
三次元測定機による精密検査のお問い合わせ
三次元測定機による精密検査についてご不明な点やご要望がございましたら、下記よりお気軽にお問合せ下さい。
<お問い合わせ先>
株式会社⼩川製作所
営業・技術担当 ⼩川宛
TEL: 03-3657-4196
FAX: 03-3673-4755
Mail: info@ogawa-tech.jp